Improving the selection process in food distribution warehouses
Palletmate
OVERVIEW
IFDA is a trade association for the food distribution industry. IFDA member companies deliver food and other products to more than 1 million professional kitchens every day.
What was our role?:
Partnering with IFDA our team was tasked with identifying areas for intervention within the warehouse that might create a positive impact on the warehouse workers while maintaining the efficiency of processes. Our team designed and tested Palletmate as a tool that would enhance warehouse selection.
IFDA x CMU
Tags: User Research, Product Design
Project Time: February 2022- May 2022
Team: Design: Me, Weiyi, Varsha Shankar
Engineering: Tianyang Lei, Weiyi Zhang
Buisness: Jasveen K., Sumairha C.
My Role: Research Lead, Design

High Turnover and Lack of Innovation in Food Distribution Warehouses
PROBLEM
Foodservice distribution warehouse jobs are physically taxing and the industry’s labor shortage is projected to continue. Our team was asked to identify a specific area of focus and develop a product concept that would be ready to go to market.

OPPORTUNITY GAP IDENTIFED
How might we improve the experience of repetitive physical labor for selectors in manual food distribution warehouses?
Palletmate: a pallet jack extension that makes picking, stacking and wrapping orders hassle-free
SOLUTION
Adjustable pallet height reduces physical strain while picking
The palletmate enables the pallet to maneuver to the right height to facilitate the selection process. Selectors can now raise the pallet to shelf height (in case of higher shelves) to quickly slide cases onto pallet.
Increased height also reduces back strain that occurs when the selector stacks cases onto the pallet.
Guard rails enhance the feeling of security
Selectors have more flexibility while stacking with the aid of adjustable guard rails that prevent cases from falling of the pallet.
The guard rails also provide stability in the event cases are not stacked properly.
Pallet rotation reduces fatigue caused by manual wrapping
Selectors can save time and energy with the pallet rotation feature that aids order wrapping which typically slows down the selectors.
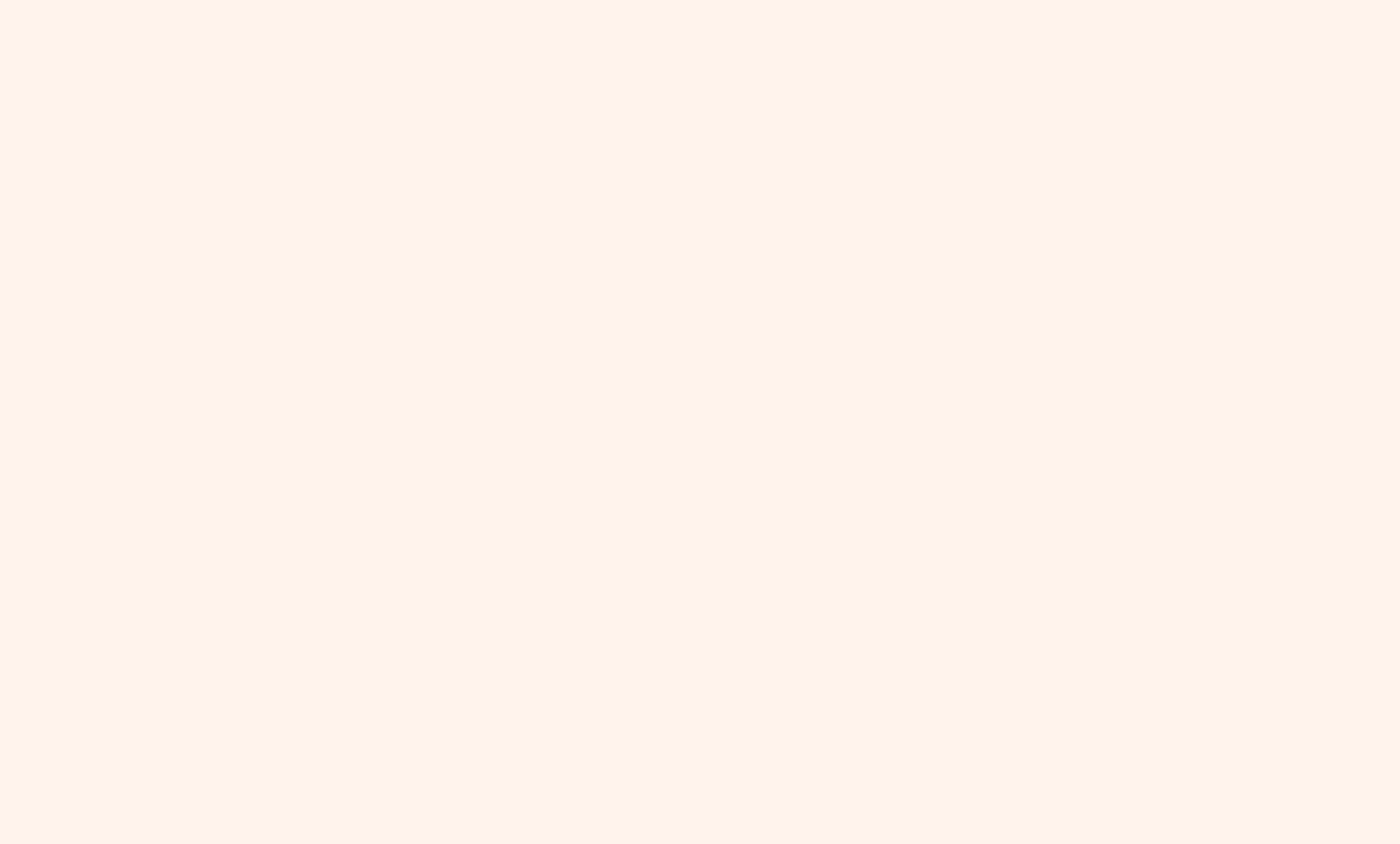
PROCESS
How did we get here?
the project was broadly segmented into 4 phases. The stages involved finding an opportunity gap, understanding the problem, ideating, prototyping/testing and creating a product launch plan the would be presented to the stakeholder.
UNDERSTANDING WAREHOUSES
Cost is a large barrier for warehouses, especially for ones that are small to medium sized, to adopt new technology
To understand warehouse operations we spoke with 7 warehouse managers across the country. We learned that pain points differed by type of warehouse (manual, semi-automatic, and automatic) and warehouse size.
Looking at the time, project feasibility, and impact, we scoped our project to focus on manual warehouses, where people had to pick cases from shelves and pack orders manually.
Selectors have the hardest job in the warehouse...and not surprisingly the highest turnover
NARROWING DOWN TARGET USERS
for the next phase of our research, we visited 2 warehouses, interviewed 10 warehouse workers, and observed the operations during the day and night shifts.
Different Roles Within the Warehouse that we studied
From our interviews, we learned that all warehouse workers must start as a selector to move up, and the selector’s job is considered the most physically tasking within the warehouse. It has the highest rate of injury and turnover.
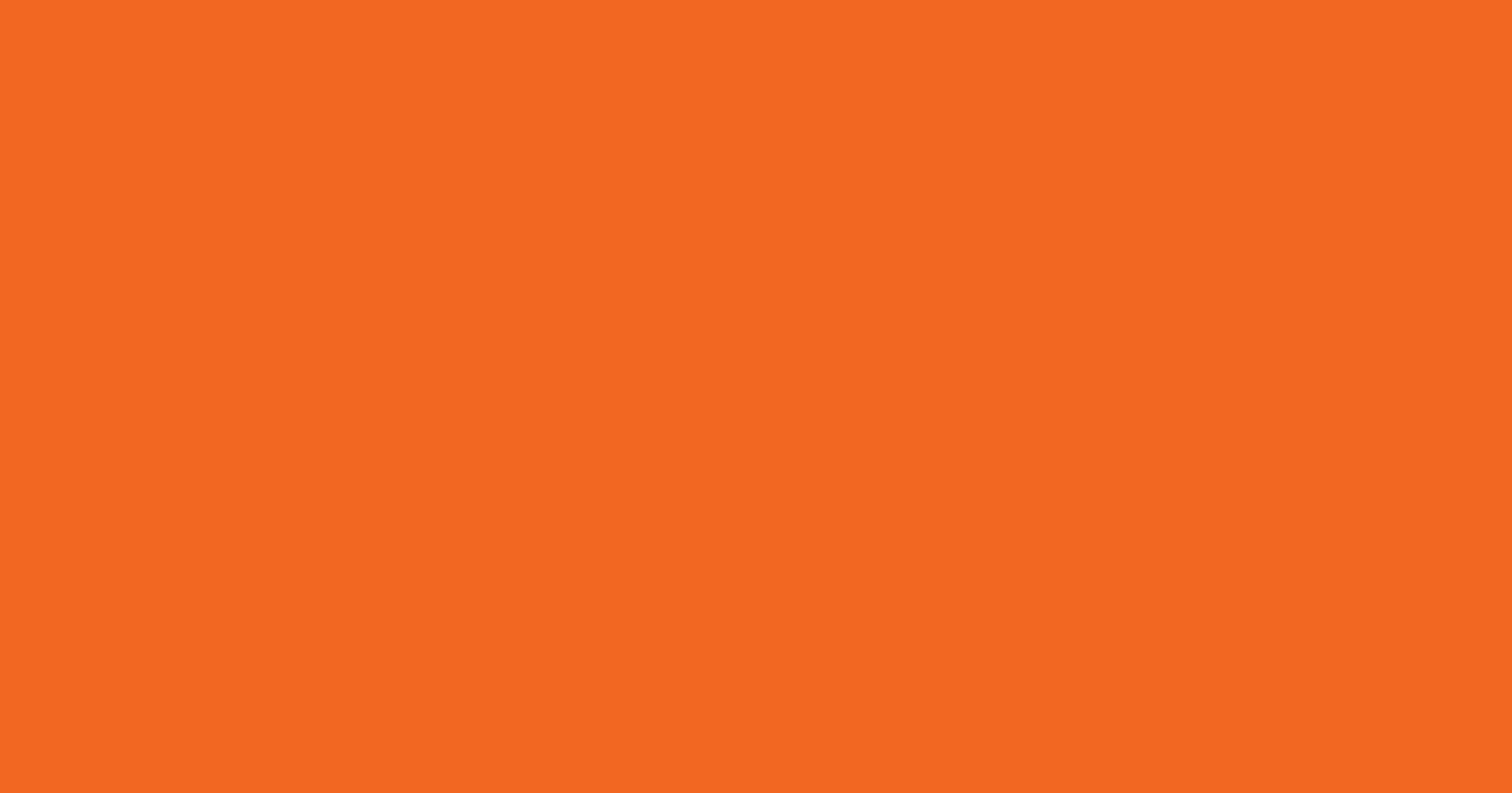
we shadowed three selectors at various stages in their career and created a journey map. Many pain points stood out to us opportunites. However at this stage it was still challenging for us to determine which part of selection we should intervene on.
Understanding the process of selection
PAIN POINTS
Selectors are fatigued mentally and physically on the job
USER INTERVIEWS
Interviews with 5 workers, comprising of selectors and former selectors (now replenishers or managers) revealed just how physically taxing the job is.
Stacking cases on the pallet is the most challenging... improper stacking leads to accidents and inefficiencies.
DISCOVERING THE PROBLEM
A co-design session with 4 selectors, the session helped us understand the logic & issues while stacking cases:
1. New selectors don’t have the expertise to be pre-emptive about their stack, leading to accidents and re-stacks mid-order.
2. Selectors may pick anywhere from 1000-1200 cases per shift, the repeated picking and stacking, coupled with the long working hours creates physical and mental fatigue.
Using the insights we gathered to form design principles
CHALLENGES & DESIGN PRINCIPLES
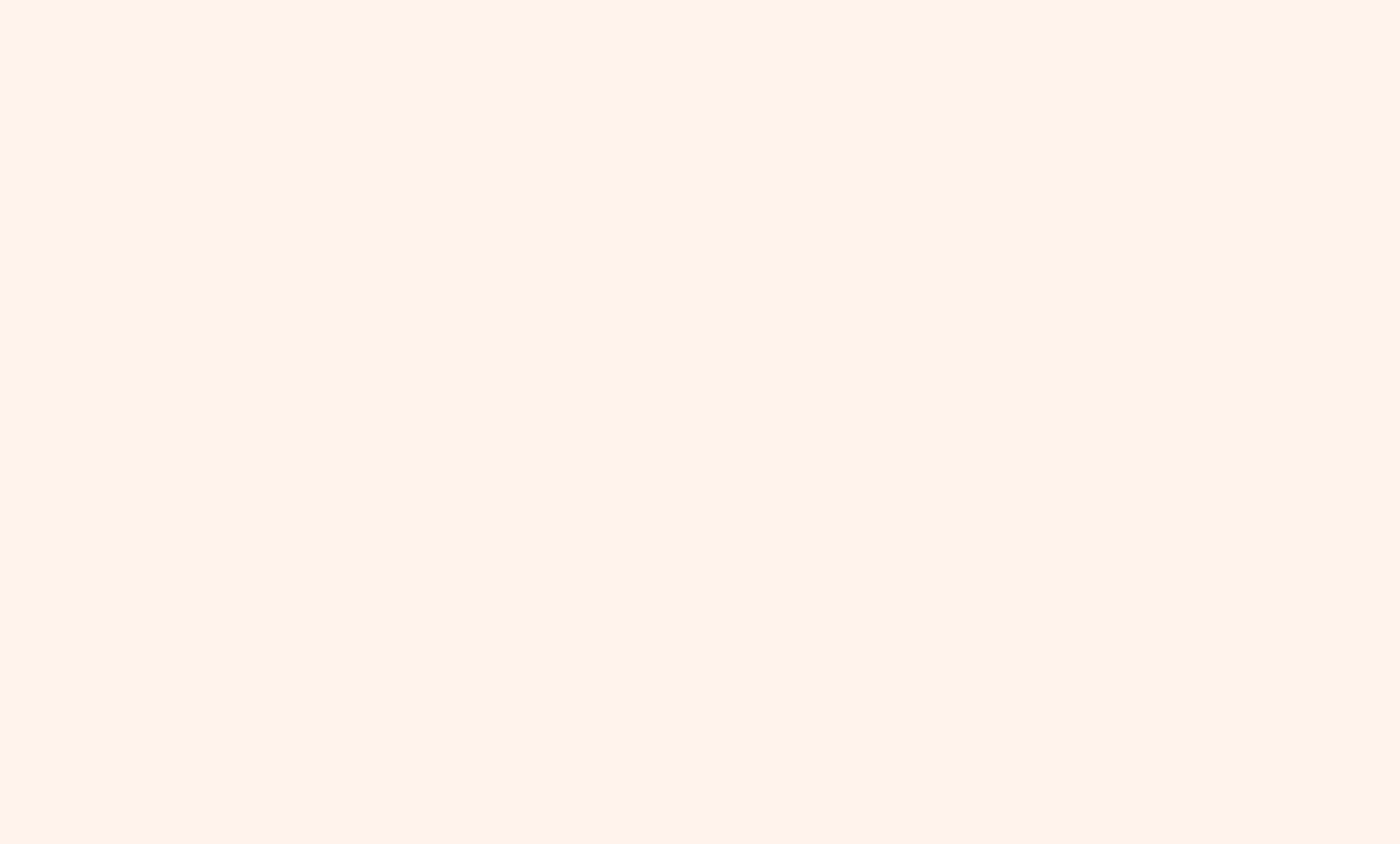
Existing products address some of the pain points, but none were versatile and fully usable all over the warehouse
COMPETITIVE ANALYSIS
We noticed there was a lack of products that could be used throughout the process of selection, certain tools existed which could only be used for specific tasks; unloading cases, wrapping cases, or placing cases on rack.
We’ve identified the problems, but how did we choose our concept?
IDEATION
From our ideation session, we clustered our concepts into three board areas:
rapid sketches of initial ideas
CONCEPT FINALIZATION
Pallet jack optimization
After pitching our top 3 ideas to the warehouse selectors, they found the pallet extension ideas to be the most useful.
They elaborated that pallet jack extensions could reduce the number of times they bend without sacrificing the selection speed
"It would be nice to have a confinement that could be used as a physical support to let stack of items to lean on"
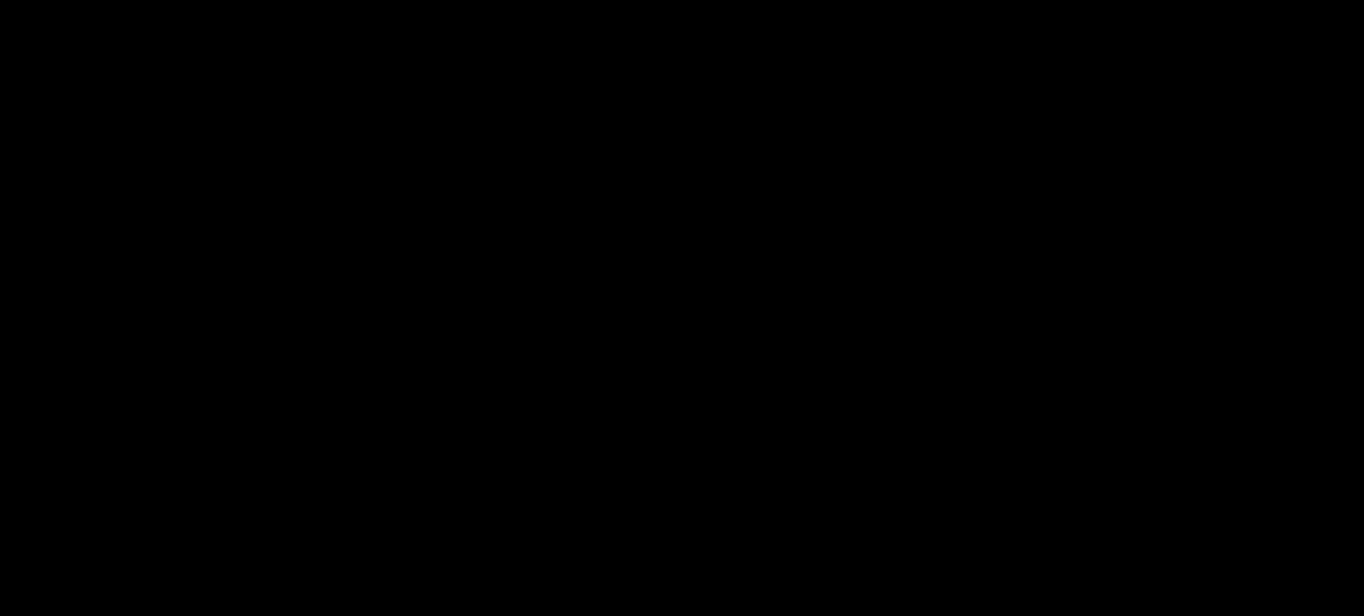
It’s getting there but not quite,
what we kept and modified
PALLETMATE V1
What worked:
1.pallet lifting
2.pallet rotation for wrapping
What needed to be changed:
1.Foot pedals to control pallet lifting were seen as inconvenient
2.Manually raised pallet barriers ended up slowing processes
3.How to trigger pallet rotation safely
PALLETMATE V2
From V1 we focused on making controls smoother, which included remote-operated control for pallet lifting and wrapping, and automated guard rails using telescopic channels.
We worked on adjusting clearance spaces to make pallet rotate safely and added a lighting element that would alert selectors before rotation is triggered
Palletmate reduces physical strain
while also increasing selection speed!
PROTYPING & USER TESTING
To validate our design we created a basic wooden prototype that features a pallet bed that could be extended and rotated, along with adjustable guard rails.
We tested each part of our design against existing conditions to see the impact of the palletmate.
pallet extension - in a test to pick 5 items with and without the palletmate, we found that selection was made easier and time taken to select one case was reduced by 5 seconds with palletmate.
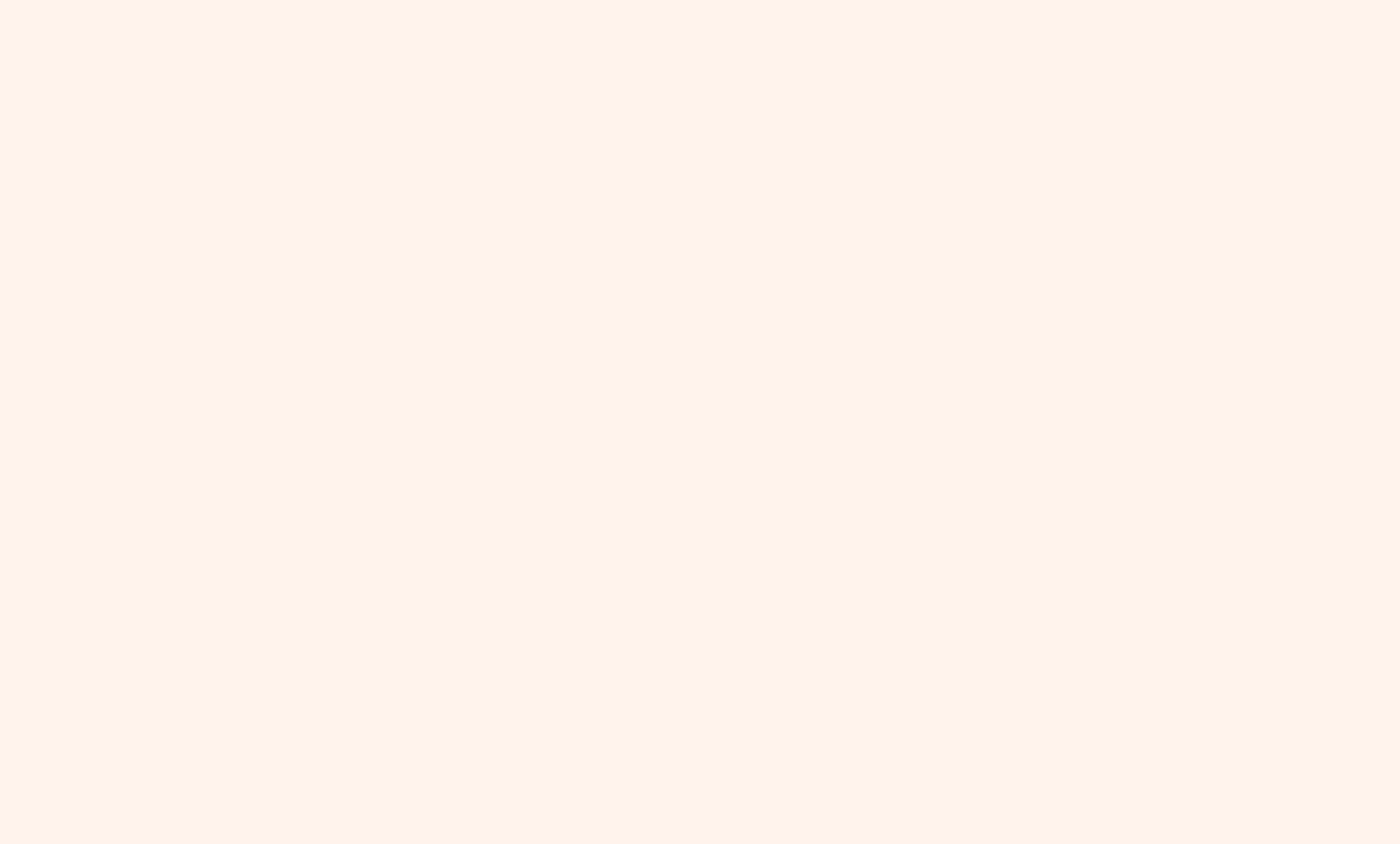
Introducing the Palletmate!
FINAL DESIGN
The Palletmate is designed to be an extension to pallet jacks used in food distribution warehouses. The Palletmate mate clips onto the prongs of the pallet jack and features the following:
Palletmate improves working conditions for selectors and saves money
IMPACT
If Palletmates were adopted in manual warehouses we found that they would save $6,500 per product
What did I learn?
REFLECTION
Interdisciplinary teams: I learned how important it is for everyone on the team to respect and understand each other’s roles while working on a project that requires the expertise of many disciplines. As a team, it was imperative we established good communication with one another to define expectations.
Communication with stakeholders: Learning that outcomes were more important than process while presenting our work to stakeholders.
Finding an opportunity: Coming into the project our team knew nothing about warehouse operations, but repetitive visits to immersive ourselves in the work of the people we were trying to help along with conversations and building a rapport with the workers helped us uncover valuable insights.